Quick Inquiry
The technology used in heat exchanger tubes is very old involving different methods of heat transfer such as radiation, convection, and conduction.
Heat exchanger tube is a device which is used to transfer heat from one medium to another for both cooling and heating processes. It separates the medium which is being used. Heat is transferred through these exchanger tubes by the conduction process. Mediums can be liquid, vapor, or gas. For example, an air-cooled heat exchanger uses air to cool a liquid and a shell & tube heat exchanger is for passing fluids.
The term ‘heat exchanger’ is mostly used when we refer to tube hear exchangers and plate heat exchangers. Refrigerators, chemical plants, air conditioners, power stations, etc. use the heat exchanging process. At times, the overall energy efficiency of a plant can be determined by these tubes. This article focuses on everything you need to know about heat exchanger tubes including the different types of tubes and their applications.
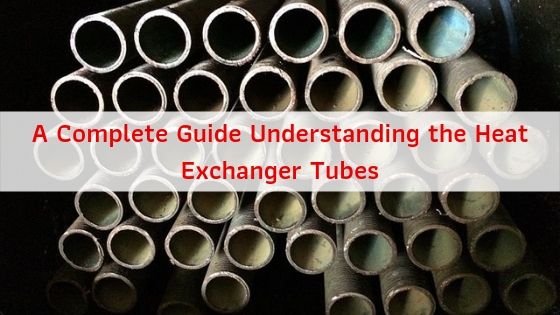
Heat Exchanger Pass
The movement of the fluid through the heat exchanger tubes is known as heat exchanger pass. Single pass is when the fluid enters from one end and exits from the other end of the heat exchanger tube. Double pass allows the fluid to enter and exit from the same end. In triple pass, the fluid passes the heat exchanger tube three times before it finally exits.
Types of Heat Exchanger Tubes & Their Characteristics
The selection of a particular heat exchanger tube depends on the rate of heat transfer. Moreover, the required heat load and temperature signify the size of the heat exchanger tubes. These can be manufactured in U-Bent shapes or Straight Lengths based on the requirements. It is interesting to know that the basic configuration of heat exchangers remain the same irrespective of their different sizes and complexities.
Based on their design characteristics, heat exchangers and their applications are classified. These characteristics define the efficiency of the tubes including some factors.
Classification Based On Flow Configuration
The movement of the flow of the fluid is also considered in heat exchanger tubes. There are four main flow configurations – 1. Parallel flow, where the fluids move in the same direction. 2. Counter flow, here the fluids move in opposite directions. This is more efficient than the parallel flow heat exchanger. 3. Cross flow, this allows the fluid to move perpendicular to each other. 4. Hybrid flow, here multiple flow passes can take place.
The rate in which the fluid flows in the exchanger tubes matters a lot. This is known as the flow rate. The capacity of heat exchanger to transfer heat increases with the increase in the flow rate. However, this also increases the mass and velocity, reducing the pressure ultimately making it a challenge to remove the energy.
Classification Based On Heat Transfer Mechanism
Heat exchanger tubes have two types of heat transfer mechanisms – single phase or two phase. There is no phase change in the first type of heat transfer process. In simple words, fluids continue to remain in the same state as they enter the heat exchanger tube. The latter type is opposite to this. It allows the fluids to change their state during the heat transfer process. Therefore, based on heat transfer mechanism, heat exchangers can be classified into four types:
- Single phase convection on both sides
- Single phase on one side and two-phase on the other side
- Two phase convention on both sides
- Radiative & combined convection heat transfer
Classification Based On Construction Method
Based on their construction methods heat exchanger tubes can be classified as the following:
Capacitive heat exchangers – Here, warm and cool fluids flow through the same channel alternately. These are basically of two types – static & dynamic heat exchangers. In the former, the heat exchanger components remain static during the flow while in the latter, the components move throughout the process.
Recuperative heat exchangers – Here, each fluid flows through its own channel simultaneously. These are basically of two types – Direct & indirect contact heat exchangers. In the former, heat transfers from one fluid to another with direct contact (fluids are not separated inside the tube), whereas, in the latter fluids flow separate inside the tube.
Components & materials used – This depends on the type of the heat exchanger and its application. Some common ones are tubes, shells, plates, fins, spiral tubes, etc.
Factors to consider while selecting a heat exchanger:
- Primary & secondary circuit liquid types
- Temperature and flow rates of both
- What is the purpose of the primary circuit
To name a few heat exchanger tubes, we have shell and tube heat exchanger, plate heat exchanger, plate and shell heat exchanger, plate fin heat exchanger, etc.
Application of Heat Exchangers
Power Plants
Heat exchangers are essential in power plants to manage thermal energy effectively. They are used for cooling turbines, maintaining optimal operational temperatures, and recovering waste heat. Applications include condensers, air preheaters, and steam generators. Efficient heat exchanger tubes improve plant performance, reduce energy costs, and ensure long-term reliability.
Chemical Processing Units
In chemical industries, heat exchangers regulate temperatures for reactions and heat recovery processes. They maintain precise thermal control, ensuring product quality and safety. Applications include distillation columns, reactors, and evaporators. Reliable heat exchanger tubes enable energy-efficient operations, reducing costs while maximising output in high-demand environments.
Steel and Fertiliser Plants
Steel and fertiliser production requires significant heat management. Heat exchangers support thermal regulation during processes like cooling molten steel or heating fertilisers. Their role extends to waste heat recovery, enhancing efficiency. With durable heat exchanger tubes, these industries achieve consistent performance under extreme temperatures and pressures.
Shipbuilding
Heat exchangers are critical in ships for managing onboard cooling and heating systems. They regulate engine temperatures, cool lubricants, and support HVAC systems. Their robust construction ensures reliability in marine environments. Efficient heat exchanger tubes are vital for fuel economy and smooth vessel operation.
Refineries
In refineries, heat exchangers enable energy transfer for high-pressure systems like boilers and heat recovery units. They cool and heat fluids during the distillation and separation processes. Advanced heat exchanger tubes withstand high temperatures, ensuring efficiency and safety in demanding refinery applications.
HVAC Systems
Heat exchangers are integral to heating, ventilation, and air conditioning (HVAC) systems in commercial and industrial settings. They regulate indoor temperatures by transferring heat between air, water, or refrigerants. High-quality heat exchanger tubes ensure energy-efficient climate control, reduce operational costs, and improve overall system performance.
Food and Beverage Industry
The food and beverage industry relies on heat exchangers for processes like pasteurisation, sterilisation, and cooling. They ensure precise temperature control to maintain product quality and safety. Durable heat exchanger tubes are critical for hygienic operations and energy-efficient heat transfer, supporting consistent production in this highly regulated sector.
Steel Plants
Heat exchangers play a crucial role in steel manufacturing by managing thermal energy during production. They cool molten steel, control furnace temperatures, and recover waste heat for reuse. Efficient heat exchanger tubes ensure smooth operations under extreme conditions, improving energy efficiency and reducing overall production costs in steel plants.
How to Choose the Right Heat Exchanger for Your Needs
Selecting the right heat exchanger tube is vital for ensuring optimal performance and cost efficiency in industrial operations. The choice depends on factors like application requirements, thermal efficiency, and budget. Below are key considerations for businesses to identify the most suitable type.
1. Understand Your Application
Evaluate the specific needs of your operation. For instance, single-tube heat exchangers are ideal for simple applications with lower heat loads, while 1 shell 2 pass heat exchangers are better suited for large-scale operations requiring multiple passes for enhanced heat transfer. Consider whether the process involves heating, cooling, or both.
2. Evaluate Flow Configuration
The flow configuration significantly impacts efficiency. A single-pass heat exchanger offers a straightforward flow path, ensuring ease of maintenance. In contrast, a two-pass heat exchanger increases the fluid’s contact with the heat transfer surface, boosting efficiency but requiring more space and resources.
3. Material and Durability
The material of the heat exchanger tube affects its performance and longevity. Choose corrosion-resistant materials like stainless steel or titanium for processes involving aggressive fluids or extreme temperatures.
4. Energy Efficiency and Maintenance
Prioritise energy-efficient designs that lower operational costs. Additionally, select a model that aligns with your maintenance capabilities to ensure long-term reliability and performance.
5. Custom Design Requirements
Mention that businesses might need to collaborate with manufacturers to customise heat exchanger designs for unique operational challenges, such as space constraints or highly specific temperature ranges.
6. Operating Pressure and Temperature
Highlight the importance of ensuring that the heat exchanger tube can withstand the operating pressure and temperature conditions of the application to prevent failures.
7. Industry-Specific Applications
Suggest that businesses consider industry-specific recommendations. For example, food-grade materials for the food industry or heavy-duty designs for petrochemical plants.
8. Scalability and Future Needs
Recommend that businesses anticipate future operational needs. A heat exchanger with scalable capacity might prove cost-effective in the long run.
9. Certifications and Standards
Emphasise the need to verify compliance with industry standards, such as ASME or TEMA, ensuring quality and safety for critical applications.
Frequently Asked Questions about Heat Exchanger Tubes
1. What factors affect the performance of a heat exchanger tube?
The performance of a heat exchanger tube is influenced by several factors, including the material used, the flow configuration, and the fluid properties. Temperature differences between the two mediums, fluid velocity, and pressure also play significant roles. Additionally, the design of the heat exchanger tube, such as its surface area and the number of passes, can impact the heat transfer efficiency.
2. How can I extend the lifespan of my heat exchanger tubes?
To extend the lifespan of heat exchanger tubes, regular maintenance is essential. This includes cleaning the tubes to prevent fouling, inspecting for corrosion or mechanical wear, and ensuring proper fluid filtration. Using corrosion-resistant materials and maintaining optimal operating conditions will also help prolong the tube’s life.
3. Can heat exchanger tubes be used for both heating and cooling?
Yes, heat exchanger tubes are versatile and can be used for heating and cooling processes. They facilitate the transfer of thermal energy between two fluids, whether for cooling a hot fluid or heating a cold one. The configuration and material choice will depend on the specific application requirements.
4. How do I determine the right heat exchanger tube size for my system?
To determine the right size, businesses should consider factors such as the desired heat transfer rate, fluid flow rates, temperature gradients, and available space for installation. Consulting with a manufacturer or an engineer can help optimise the size and configuration of the heat exchanger tube for specific system requirements.
Increase The Life Span of a Heat Exchanger
There are certain ways which can help increase the life time of a heat exchanger. The design data has to be accurate. It will enhance the thermal efficiency and also increase the life of the heat exchanger. Another point to consider is the filling and pipe work. Moreover, with regular maintenance and service life span of the heat exchangers can increase.
The thermal energy required for heating or cooling a liquid is also provided by the heat exchangers.
Anand Seamless Ltd is a leading heat exchanger manufacturer. We have the expertise and resources to produce and supply premium quality seamless tubes.
For more information about our products, please call us at +91-9099996851. We’ll be happy to assist you!
lATEST BLOG |
The Impact of Tube Fin Design on Heat Transfer Performance
Finned tubes are essential in industries like powe |
U-Tube vs. Straight-Tube Heat Exchangers: Comparison Guide
Heat exchangers play a crucial role in industries |
Destructive vs. Non-Destructive Testing for Seamless Tubes
Seamless tubes play a critical role in industries |
The Hidden Costs of Poor-Quality Heat Exchanger Tubes: A Manufacturer’s Perspective
Heat exchangers play a critical role in various in |
Seamless Tubes in Boiler and Power Plants: Why They Are a Game-Changer
Seamless tubes are crucial in various industrial a |