Quick Inquiry
In the world of heat exchange technology, aluminium finned tubes play a crucial role in various industries, offering efficient heat transfer solutions. As a leading heat exchanger tube manufacturer in India, we understand the importance of grasping the fundamentals of aluminium finned tubes for businesses seeking optimal performance in their operations. This guide aims to provide comprehensive insights into the basics, equipping businesses with the knowledge needed to make informed decisions for their applications.
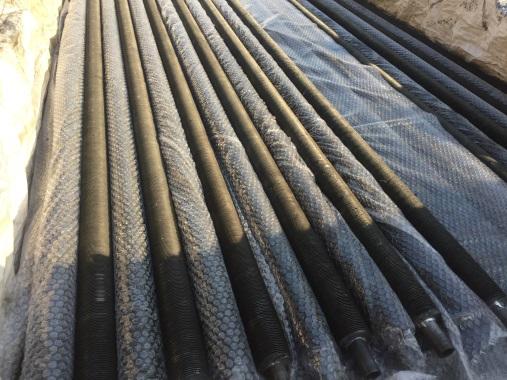
What is an Aluminium Finned Tube?
Aluminum finned tubes are specialised heat exchanger components designed to enhance heat transfer efficiency in various heating, ventilation, air conditioning, and refrigeration (HVAC&R) systems. These tubes consist of a core tube typically made of materials like copper, stainless steel, or aluminium, with aluminium fins attached along the length of the tube’s exterior surface. The primary function of the fins is to increase the surface area available for heat transfer between the fluid inside the tube and the surrounding air or fluid. This increased surface area promotes greater heat exchange, allowing for improved thermal performance and energy efficiency.
Aluminium is chosen as the fin material due to its excellent thermal conductivity, lightweight nature, corrosion resistance, and affordability. These properties make aluminium finned tubes suitable for a wide range of applications across diverse industries, including power generation, chemical processing, automotive, and aerospace.
In addition to standard straight fin configurations, the finned tubes are available in various designs such as helical, embedded, and serrated fins, each offering specific advantages depending on the application requirements.
Benefits of Aluminium Finned Tubes
Aluminum finned tubes offer a multitude of advantages that make them a preferred choice for businesses operating in various industries. Understanding these benefits is crucial for maximising the efficiency and effectiveness of heat exchange systems. Let’s delve into the key advantages of aluminium finned tubes:
1. Cost-Effective:
Aluminum finned tubes are highly cost-effective compared to alternative materials like copper or stainless steel. Aluminium is abundant, resulting in lower material costs. Additionally, its lightweight nature reduces transportation and installation expenses. Businesses can achieve significant cost savings without compromising on performance.
2. Corrosion-Resistant:
Corrosion can significantly degrade the performance and lifespan of heat exchanger components. Aluminum finned tubes boast exceptional corrosion resistance, even in harsh operating environments. This corrosion resistance ensures longevity and reliability, reducing the need for frequent replacements and maintenance.
3. Lightweight:
Aluminum is renowned for its lightweight properties, making the finned tubes easy to handle, transport, and install. This characteristic is particularly advantageous in applications where weight is a concern, such as aerospace or automotive industries. The lightweight nature of the tubes simplifies logistics and lowers structural support requirements.
4. Low Maintenance:
Minimising maintenance requirements is crucial for enhancing operational efficiency and reducing downtime. Aluminum finned tubes demand minimal maintenance compared to alternative materials. Their corrosion-resistant properties eliminate the need for protective coatings or frequent cleaning, saving time and resources for businesses.
5. Versatile:
Aluminum finned tubes offer versatility in design and application, catering to diverse heat exchange requirements across various industries. They can be tailored to specific performance criteria, including heat transfer efficiency, airflow resistance, and pressure drop. Whether used in HVAC systems, refrigeration units, or industrial processes, these tubes deliver reliable performance across a wide range of applications.
6. Limited Temperature Range:
While aluminium finned tubes excel in many aspects, it’s essential to consider their limited temperature range compared to other materials. Aluminum has a lower melting point and is less suitable for high-temperature applications exceeding certain thresholds. However, within their temperature limits, the tubes provide exceptional performance and reliability.
Different Types Of Aluminium Finned Tubes
Aluminium finned tubes come in various configurations, each tailored to specific heat transfer requirements and application demands. Understanding the different types is essential for businesses seeking optimal performance and efficiency in their heat exchange systems. Let’s explore the various types in detail:
1. Helical Aluminum Finned Tubes:
Helical finned tubes feature fins that spiral around the outer surface of the tube in a helical pattern. This design maximises the surface area available for heat transfer while promoting efficient fluid flow. Helical fins offer excellent heat transfer performance and are commonly used in air-cooled heat exchangers, refrigeration systems, and process heaters. The helical configuration enhances turbulence and disrupts laminar flow, enhancing heat transfer efficiency.
2. L-Type Aluminum Finned Tubes:
L-type finned tubes are characterised by fins that are pressed or welded onto the outer surface of the tube in a perpendicular “L” shape. This configuration provides increased surface area for heat exchange while maintaining structural integrity. The tubes are widely used in applications where space constraints or airflow considerations are paramount, such as air conditioning units, heat pumps, and condensers.
3. Low-Finned Tubes:
Low-finned tubes, also known as extended surface tubes or integral finned tubes, feature fins that are integral to the tube wall. This results in a significantly larger surface area compared to standard tubes. These fins are formed by extruding the tube wall, creating a series of low-profile fins. The tubes offer enhanced heat transfer performance and are commonly utilised in applications requiring high thermal efficiency, such as heat exchangers for power generation, chemical processing, and oil refineries.
4. Knurled Aluminum Finned Tubes:
Knurled finned tubes feature fins with a knurled or serrated surface texture, providing increased turbulence and enhancing heat transfer efficiency. The knurled surface disrupts boundary layers and promotes mixing, improving heat transfer coefficients. The tubes are often used in applications where enhanced heat transfer performance is critical, such as heat exchangers for air conditioning and refrigeration.
5. Extruded Aluminum Finned Tubes:
Extruded aluminium finned tubes are manufactured by extruding aluminium fins onto the outer surface of a base tube. This process creates a strong mechanical bond between the fins and the tube, ensuring durability and reliability. The tubes are popular for their high heat transfer efficiency, lightweight construction, and corrosion resistance. They find extensive use in air-cooled heat exchangers, condensers, and evaporators across various industries.
6. Embedded Aluminum Finned Tubes:
Embedded aluminium finned tubes feature fins that are embedded or inserted into grooves or channels on the outer surface of the base tube. This design provides increased structural integrity and ensures excellent thermal contact between the fins and the tube. The tubes offer enhanced heat transfer performance and are commonly employed in applications requiring high thermal conductivity, such as heat exchangers for refrigeration, HVAC systems, and industrial processes.
Commonly Asked Questions
1. What are the key factors to consider when selecting the right type of aluminium finned tube for my application?
When choosing an aluminium finned tube, factors such as operating temperature, fluid compatibility, airflow requirements, space constraints, and desired heat transfer efficiency should be taken into account. Additionally, consider the specific industry standards and regulations applicable.
2. How do I determine the optimal fin density for my heat exchanger?
The fin density of aluminium finned tubes significantly influences heat transfer performance. It is typically determined based on the heat transfer coefficient required for the application and the available airflow or fluid velocity. Higher fin density results in increased surface area and improved heat transfer efficiency, but it may also lead to higher pressure drop and airflow resistance.
3. Are aluminium finned tubes suitable for corrosive environments?
Aluminum tubes exhibit good corrosion resistance, particularly in mild to moderate corrosive environments. However, in highly corrosive conditions, such as those involving acidic or alkaline fluids, it may be necessary to consider alternative materials or protective coatings to enhance durability and longevity.
4. Can aluminium tubes be customised to meet specific application requirements?
Yes, aluminium finned tubes can be customised in terms of dimensions, fin geometry, material thickness, and surface treatments to accommodate unique application needs. Working closely with a reputable manufacturer can help ensure the tubes are tailored to meet your exact specifications and performance criteria.
We Manufacture Aluminum Finned Tubes With Customised Specifications
Experience the difference of tailored solutions with our aluminium finned tubes designed to meet your exact operational requirements. At Anand Seamless Ltd, we specialise in manufacturing variety of heat exchanger tubes with customisable specifications, ensuring optimal performance and efficiency for your heat exchange systems.
Our team of experts collaborates closely with you to understand your specific application needs. Whether it’s maximising heat transfer efficiency, enhancing corrosion resistance, or meeting space constraints, we have you covered. With state-of-the-art manufacturing facilities and advanced technology, we can produce aluminium finned tubes in a wide range of dimensions, fin geometries, and material thicknesses.
By choosing Anand Seamless Ltd, you gain access to high-quality tubes that are precision-engineered to deliver exceptional performance and reliability in diverse industries and applications. Whether you’re in the HVAC, refrigeration, power generation, or chemical processing industry, our customised solutions are tailored to exceed your expectations.
Don’t settle for off-the-shelf solutions that only partially meet your needs. Partner with us and experience the difference between personalised service and superior quality aluminium-finned tubes. Contact us at +91-9099996851 or write to us at inquiry@anandseamless.com to discuss your requirements and discover how we can optimise your heat exchange systems for maximum efficiency and productivity.
lATEST BLOG |
The Impact of Tube Fin Design on Heat Transfer Performance
Finned tubes are essential in industries like powe |
U-Tube vs. Straight-Tube Heat Exchangers: Comparison Guide
Heat exchangers play a crucial role in industries |
Destructive vs. Non-Destructive Testing for Seamless Tubes
Seamless tubes play a critical role in industries |
The Hidden Costs of Poor-Quality Heat Exchanger Tubes: A Manufacturer’s Perspective
Heat exchangers play a critical role in various in |
Seamless Tubes in Boiler and Power Plants: Why They Are a Game-Changer
Seamless tubes are crucial in various industrial a |