Quick Inquiry
Seamless tubes are widely used in various industries such as automotive, oil and gas, power generation, and construction due to their exceptional properties, such as high strength, durability, and resistance to corrosion. However, the manufacturing process of seamless tubes can vary, and each process can produce tubes with different properties and characteristics.
This article explores the differences between hot-rolled, cold-rolled, and cold-drawn tubes, their properties, advantages, and disadvantages, and which one to choose based on your specific needs.
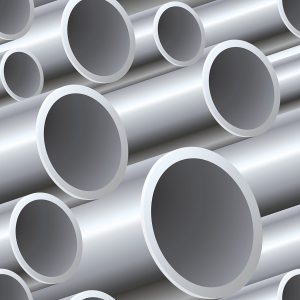
Hot-Rolled Seamless Tubes
These are manufactured using a hot-rolling process, where the tubes are heated above their recrystallization temperature and rolled to the desired size and thickness. Hot-rolled seamless tubes are primarily made from carbon steel and alloy steel.
Properties
- High dimensional accuracy: Hot rolling process produces tubes with uniform dimensions and thickness.
- Superior surface finish: The surface finish is smooth and has fewer defects.
- Excellent mechanical properties: Hot rolled tubes have high strength, durability, and toughness.
- Greater strength and durability: The manufacturing process of the tubes results in a denser and stronger metal structure.
- Uniformity in shape and size: The hot rolling process produces tubes that are consistent in shape and size.
Different Uses
- Structural applications: Hot-rolled seamless tubes are used in structural applications, such as construction and building.
- Industrial machinery and equipment: These tubes are used in manufacturing equipment, such as cranes, conveyors, and processing machinery.
- Oil and gas pipelines: They are used in the construction of pipelines for transporting oil and gas.
- Heat exchanger tubes: They are applicable in the fabrication of heat exchangers, which play a vital role in cooling or heating fluids by transferring heat between them.
- Automotive industry: They are used in the production of automotive parts, such as axles, drive shafts, and suspension components.
Advantages
- Cost-effective manufacturing process: Hot rolling is a cost-effective method of producing seamless tubes.
- High production rate: Hot rolling produces tubes at a high production rate.
- Superior mechanical properties: The tubes have high strength, durability, and toughness.
- Consistency in shape and size: The hot rolling process ensures consistency in the shape and size of the tubes.
Disadvantages
- Limited design flexibility: The hot-rolling process limits the ability to produce tubes with complex shapes and designs.
- Limited control over internal and external surface quality: The surface quality of hot-rolled tubes is not as smooth as that of cold-drawn and cold-rolled tubes.
- High temperatures: During the manufacturing process can result in the formation of scale and surface defects.
Cold-Rolled Seamless Tubes
These are produced by cold drawing a hollow cylindrical steel bar through a die, reducing the tube’s diameter and thickness. The process involves annealing the steel at a lower temperature, which improves its mechanical properties.
Properties
- Excellent dimensional accuracy: The cold-rolling process produces tubes with tight dimensional tolerances.
- Higher surface finish quality: The surface finish of cold-rolled seamless tubes is smoother than that of hot-rolled counterparts.
- Better internal and external surface quality: The tubes have fewer surface defects and smoother internal surfaces.
- Superior mechanical properties: They have higher strength, toughness, and ductility.
- Enhanced formability and ductility: The cold rolling process improves the formability and ductility of the steel.
Different Uses
- Aerospace industry: These tubes are used in the production of aircraft parts, such as hydraulic lines and fuel lines.
- Hydraulic systems: Cold-rolled seamless tubes are used in the construction of hydraulic systems.
- Power generation equipment: These tubes are used in the construction of power generation equipment, such as boilers and heat exchangers.
- Automotive industry: They are used in the production of automotive parts, such as steering columns and drive shafts.
- Heat exchanger tubes: They are used in the construction of heat exchangers for cooling or heating fluids.
Advantages
- Superior dimensional accuracy: Cold rolled tubes have tight dimensional tolerances, making them suitable for applications that require high precision.
- Better surface quality: The tubes have a smoother surface finish than their hot-rolled counterparts.
- Improved mechanical properties: Cold rolling process improves the strength, toughness, and ductility of the steel.
- Enhanced formability and ductility: They have better formability and ductility than hot-rolled ones.
Disadvantages
- Higher manufacturing costs: Cold rolling is a more expensive manufacturing process than hot rolling.
- Longer lead times: The manufacturing process of cold-rolled seamless tubes takes longer than hot-rolled counterparts.
- Limited production volume: The cold rolling process is not suitable for large-volume production.
Cold Drawn Seamless Tubes
These are metal tubes made from a solid cylindrical metal bar pulled through a die to create a seamless and smooth surface. The process is carried out at room temperature, which results in increased strength and dimensional accuracy.
Properties:
- Excellent dimensional accuracy: The cold drawing process produces tubes with tight dimensional tolerances.
- Superior surface finish quality: Cold-drawn tubes have the smoothest surface finish among all seamless tubes.
- Better internal and external surface quality: The tubes have fewer surface defects and smoother internal surfaces.
- Superior mechanical properties: They have the highest strength, toughness, and ductility among all other counterparts.
- Enhanced formability and ductility: The cold drawing process improves the formability and ductility of the steel.
Different Uses:
- Precision engineering applications: These tubes are used in precision engineering applications, such as machine parts and instrumentation.
- Hydraulic systems: Cold-drawn tubes are used in the construction of hydraulic systems.
- Oil and gas industry: These tubes are used in the production of oil and gas drilling equipment, such as drill bits and pumps.
- Automotive industry: They are used in the production of high-performance automotive parts, such as racing car parts and engine components.
- Heat exchanger tubes: They are applicable in manufacturing heat exchangers that facilitate heat transfer between fluids.
Advantages:
- Superior dimensional accuracy: The seamless tubes have tight dimensional tolerances, making them suitable for applications that require high precision.
- Better surface quality: The tubes have the smoothest surface finish among all other variations.
- Improved mechanical properties: They have the highest strength, toughness, and ductility.
- Enhanced formability and ductility: They have better formability and ductility than hot-rolled and cold-rolled versions.
Disadvantages:
- Higher manufacturing costs: Cold drawing is the most expensive manufacturing process among all seamless tubes.
- Longer lead times: The manufacturing process of cold-drawn tubes takes longer than hot-rolled and cold-rolled tubes.
- Limited production volume: The cold drawing process is not suitable for large-volume production.
Comparison Chart: Cold Drawn vs. Hot Rolled vs. Cold Rolled Seamless Tubes
Product | Cold Drawn Tubes | Hot Rolled Tubes | Cold Rolled Tubes |
Production Process | Cold drawn process | Hot rolling process | Cold rolling process |
Surface Finish | Smooth and bright | Slightly rough | Slightly rough |
Dimensional Accuracy | High | Moderate to low | High |
Mechanical Properties | High | High | Moderate |
Cost | High | Moderate | High |
Production Volume | Low | High | High |
Applications | High-performance applications such as aerospace, automotive, and machinery | General-purpose applications such as construction, infrastructure, and transportation | Applications where dimensional accuracy and surface finish are critical, such as bearings, cylinders, and hydraulic systems |
It is important to note that the properties and applications of seamless tubes may vary based on the specific material and manufacturing process. It is crucial to consult with a trusted seamless pipes and tubes supplier for exact specifications.
Which Seamless Tubes Should You Choose?
There is no one-size-fits-all solution when choosing the right seamless tube for your application. Each type of tube has its own unique properties, advantages, and disadvantages. It is essential to consider factors such as mechanical properties, dimensional accuracy, surface finish, and production volume before making a decision.
Consulting with a trusted and experienced seamless tubes and pipes supplier can help you choose the right product for your application. By understanding the properties and applications of hot-rolled, cold-rolled, and cold-drawn tubes, you can make an informed decision and ensure the optimal performance of your equipment.
Order Now for Top-Quality Seamless Pipes from Anand Seamless Ltd
If you are in need of high-quality seamless pipes or tubes for your application, look no further than Anand Seamless Ltd. We are a trusted manufacturer and supplier of a wide range of products, including carbon steel seamless tubes, alloy steel seamless tubes, and heat exchanger tubes. With a commitment to quality and customer satisfaction, we use state-of-the-art manufacturing technology and equipment to produce products that meet the highest industry standards.
We understand the importance of timely delivery and competitive pricing. Thus, we strive to provide our customers with a hassle-free experience, from ordering to delivery. Our team of experienced professionals is dedicated to providing personalized support and technical guidance to ensure you get the right seamless pipes or tubes for your application.
Contact Anand Seamless Ltd today, explore a broad range of the best quality products, and experience our exceptional customer service.
lATEST BLOG |
What Are Fuel Injection Tubes? A Beginner’s Guide
Fuel injection systems are a crucial component in |
What Distinguishes a Custom-Solution Heat Exchanger Manufacturer?
In industries where heat transfer plays a pivotal |
Hydraulic Cylinder Tube Finishes: Why Honing and Polishing Are Essential
In hydraulic systems, efficiency and reliability a |
Guide to Intercooler Tubes and How They Work
Intercooler tubes play a critical role in modern i |
Why Are SA 179 Tubes a Popular Choice for Marine Applications?
SA 179 tubes are an integral part of the marine in |